North American broadline food and beverage company’s batch and sortation control upgrade
The Challenge
The food and beverage distributor sought to enhance their outbound batch and sortation controls, both of which needed updates and improved functionality. As the company already had a warehouse management system and a real time floor control programmable logic controller (PLC) device, Matthews Compass needed to implement a software system that gave the operation complete control over outbound batch and sortation control mechanisms.The Strategy
To provide a modern and reliable controls and software system solutions, Compass offered a user-friendly graphical interface to act as a supervisory-level software system for the control of the outbound conveyor system. The primary capabilities and functionalities of this software system included:- Batch management
- Sortation control
- Wonderware human machine interface (HMI)
- Graphical control stations for operators
- Easy-to-use status information for maintenance personnel
The Solution
In order to maintain the sequence of cartons being picked in the pick modules, Compass proposed to provide the batch control functions with the base Compass Order Routing System (CORS) product. The CORS batch control monitored, displayed, and controlled the release of cartons from the facility’s pick modules and central merge, as well as integrating with existing floor-level PLCs to provide a complete batch sequencing system.
CORS served many purposes for operations management, providing them with the following batch and sortation control information:
- Scanner statistics – Provided maintenance personnel insight into the current sort scanner performance.
- Divert counts – Allowed operations to view counts of packages diverted to each chute for the current shift, and the reasons for non-diverts. Counts for all chutes, including reject, unassigned, and no-read lanes are displayed.
- Rate monitor – Enabled the operator to view percentages, counts, and rates of packages that were scanned, sorted and unsorted, and packages that were not diverted based on PLC I/O and logic overriding the divert assignment. It also detailed the current rate in a meter graphic along with the minimum, average, and peak rate (packages per minute).
- Historical scanner statistics – Granted maintenance personnel the ability to view scanner statistics over a configurable period of time.
The End Result
Upon project completion, the food and beverage distribution center had a new batch control and sortation system. With Compass’ CORS software, operations managers can more accurately monitor and interact with their controls system.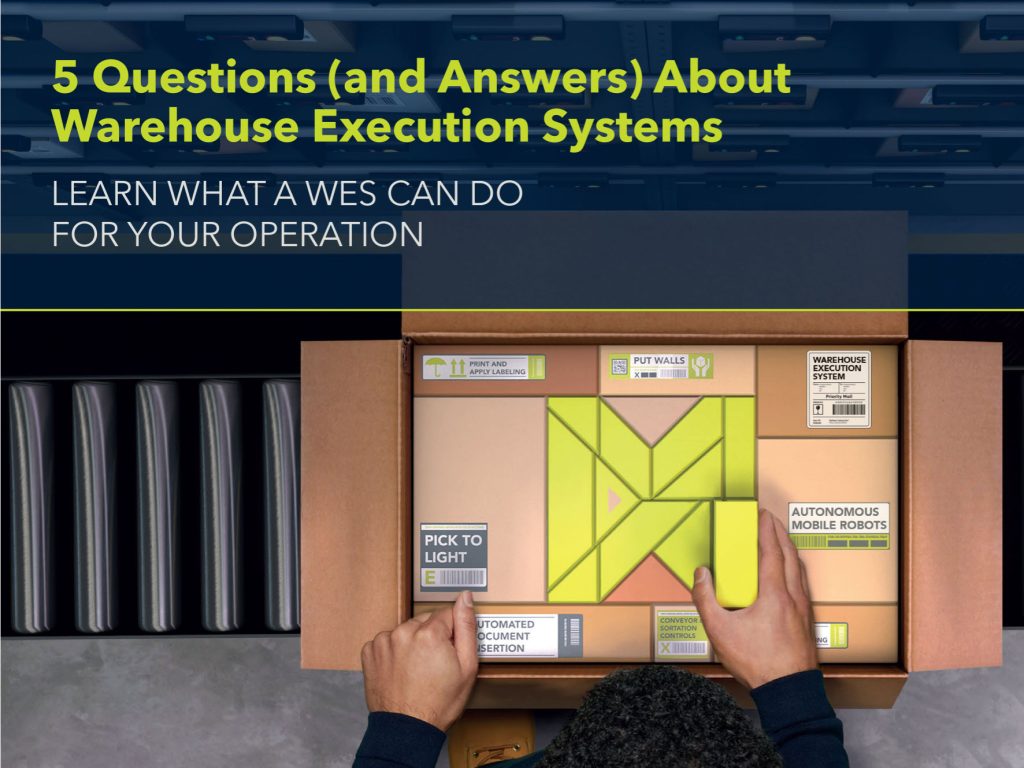
WES EBOOK
5 questions and answers about Warehouse Execution Systems.
Learn what our WES can do for your operation.