
Integrating Robotics in Distribution Centers
AMRs are “autonomous” mobile robots. But that does not mean that they are independent of other systems. A lot goes into an optimized, synergistic integration with other systems because each distribution center’s operations are different. Each DC’s technology stack, combined with its MHE, is unique.
You may be daydreaming of “plug and play” robotics, and many robotics suppliers are promising just that. However, take a moment to consider – how should you optimize robotics to fit within your existing technological operations to not only connect and “play nice” together, but also to fully realize their highly-touted capabilities? And, not to mention, improve the performance of your entire operation at the same time?
Plug and play, or not, it still requires engineers, programmers and software integration in order to implement your chosen robotic technology, to deploy it for future “autonomy” within your distribution center.
Installing robotics to reach a promised ROI is only as successful as the integration to your WMS, WES and other systems, and how they communicate and interact with other people and equipment.
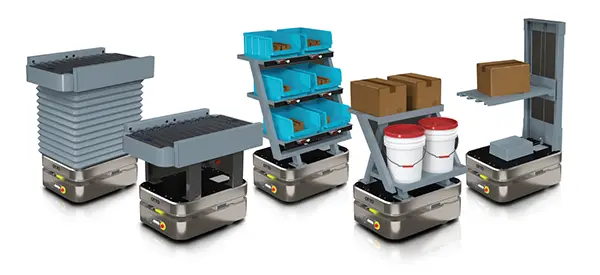
- Am I working with a company who knows warehouse automation and how to optimize my DC as a whole?
- Is it their goal to maximize my DC’s efficiency, throughput and more, taking into account all types of material handling equipment and technology I employ? (Using the right execution software to optimize robotic technologies in harmony with whole system is key.)
- Consider the following 4 examples of material handling integrations using robotics:
1 – Goods-to-Person
Traditionally DCs use person-to-goods picking, where employees travel to product storage locations to select items for orders. Lately more DCs are moving towards goods-to-person (GTP) applications, where products required for an order are automatically transported to employees for picking. When labor is difficult to find, GTP enhances employee productivity by allowing them to focus on picking or other value-added tasks while automation handles basic product movement. Goods-to-person systems are scalable to meet growing demand or SKU count. They also increase speed and efficiency in high-volume ecommerce and omnichannel fulfillment operations where customers expect immediate, flawless delivery. Automated storage and retrieval systems (ASRS) and autonomous mobile robots (AMRs) are two popular technologies used to execute GTP processes. You can read more about GTP integrations in this blog.
2 – AMR Integration
- Autonomous mobile robot (AMR) cart-based picking, like RF cluster picking and integrated light-directed picking. The warehouse execution system (WES) interfaces with the AMR Fleet Management System to create pick tasks, distribute them to the AMR fleet and execute picks – resulting in up to 3X picking efficiency.
- AMRs can increase the efficiency of other order fulfillment methodologies and equipment like order picking carts. Matthews has provided thousands of automated picking carts with pick-to-light, RF, label printing and other technologies to make operations like batch picking more efficient. Today, AMRs can autonomously move the carts throughout the distribution center to where picks are needed. This frees human employees to focus on higher value tasks like picking vs. manual material transport.
- AMR attachments enhance existing operations without facility disruption or reconfiguration, significantly improving throughput efficiency, while immediately reducing errors. The right AMR attachment dynamically integrates AMRs robots into a system to compliment existing human operators and automation. You can see the variety of application-specific AMR tops available here.
3 – Robotic Arm Integration
Robotic arm applications, such as robotic put walls and palletization, compliment manual processes and enable fully-automated facility operations. WES software passes data and instructions to the robotic arm. It also assigns and tracks SKUs to pallet positions and cubby locations. The resulting flexible sortation system reduces labor issues, and improves overall productivity.
4 – Robotic Case Packing Integration
The WES interfaces to robotic packing cells to pass data and instructions. The software manages autoboxing of manufactured products coming directly from production lines. Through the process, the WES tracks the product through the automated packaging and prints and applies case labels to the finished cases. This reduces opportunities for human error and reliance on seasonal labor by up to 75%.
These were just a few examples of specific robot integrations and their outcomes for the entire DC’s operations.
What types of integrations are you considering for your operations?
While Matthews is known for robust warehouse execution systems (WES), integrated controls and light-directed technologies, we have already enhanced robotics operations within a number of systems spanning multiple industries such as:- E-commerce
- 3PL
- Medical Supplies
- Food and Beverage/E-grocery
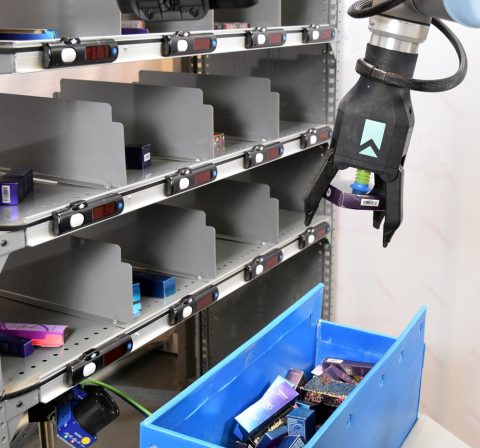