Goods to Person
Traditionally DCs use person-to-goods picking, where employees travel to product storage locations to select items for orders. Lately more DCs are moving towards goods-to-person (GTP) applications, where products required for an order are automatically transported to employees for picking. When labor is difficult to find, GTP enhances employee productivity by allowing them to focus on picking or other value-added tasks while automation handles basic product movement. Goods-to-person systems are scalable to meet growing demand or SKU count. They also increase speed and efficiency in high-volume e-commerce and omnichannel fulfillment operations where customers expect immediate, flawless delivery. Automated storage and retrieval systems (AS/RS) and autonomous mobile robots (AMRs) are two popular technologies used to execute GTP processes.
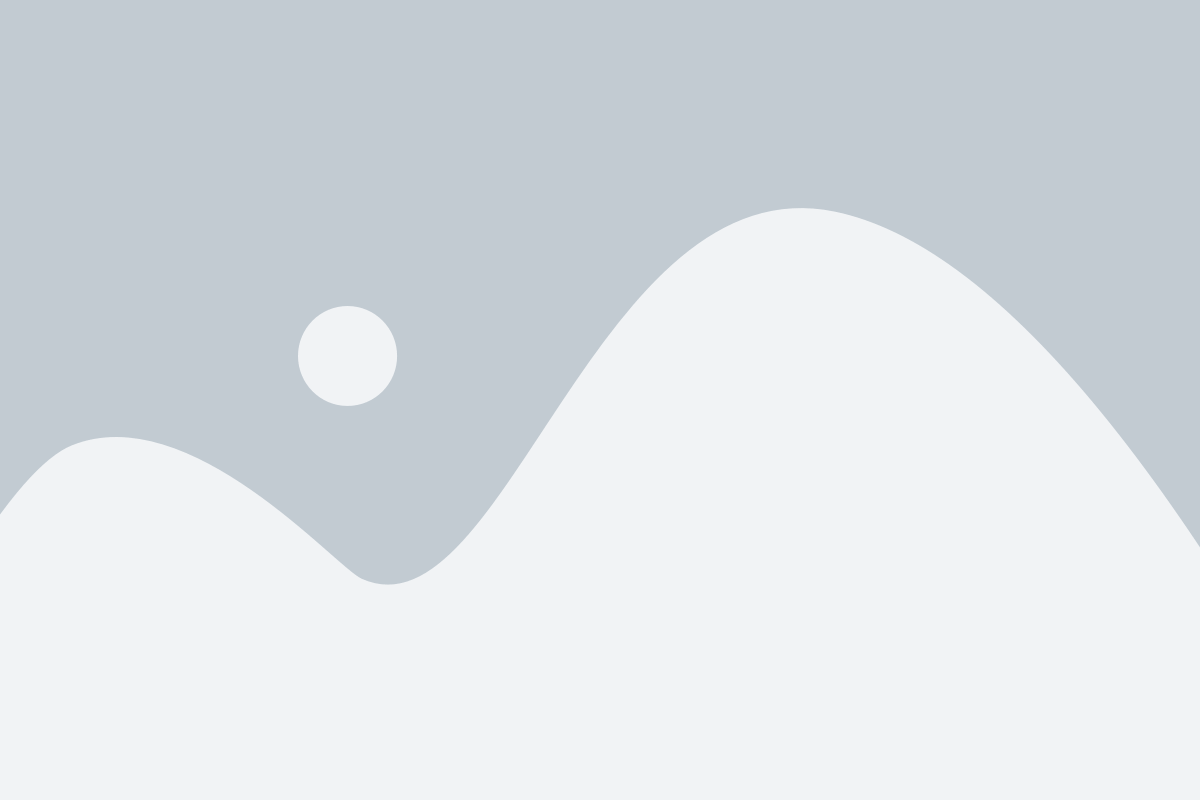
Goods-to-person applications often use automated storage and retrieval systems (ASRS or often AS/RS) like shuttles or mini-load ASRS to bring cartons or totes of products from high-density storage to workstations for picking. With ASRS, distribution centers can use more of their vertical cube and ‘go up’ for additional storage, especially useful now that distribution center space is at a premium. ASRS also maintain better inventory count and quality. Products are delivered to employees at ergonomically designed workstations, increasing their productivity and accuracy.
Matthews NEXUS warehouse execution system has integrated many leading ASRS solutions with other warehouse automation in the facility. NEXUS WES software uses real-time data and adaptive learning to enhance throughput by continuously adjusting resources, based on rate and projected workflow. NEXUS may, for example, balance work by routing some orders from an ASRS to a robotic picking arm, while others go to a pick-to-light area where products like Matthews Lightning Pick, which has been integrated with top ASRS providers, can boost pick rate productivity, or offer put walls for fast order sortation.
Diminished labor resources and increased ecommerce demand are also driving the adoption of autonomous mobile robots (AMRs). Like ASRS, the AMRs eliminate the need for employees to walk throughout a DC looking for the right merchandise. AMRs are more flexible for facility layout changes than large conveyor systems, so they’re very scalable.
With NEXUS, Matthews has integrated a variety of these best-of-breed technologies for picking, sorting and material transport. Matthews also offers application-specific toppers for the AMRs, enabling exciting new possibilities. For years, Lightning Pick carts have helped employees batch-pick multiple orders with each pass through the DC. Now order waves can move autonomously throughout the distribution center instead of being pushed by a human, allowing people to focus on the greater value task of picking orders.
AMRs can also deliver totes or cartons of product to put walls for goods-to-person sortation applications. Lights on the AMR top, or projection picking systems, can guide employees to the right totes. From there, lights on the put walls guide employees to fill the correct ecommerce or direct-to-consumer order.