In the fast-paced world of order fulfillment, operational uptime is the backbone of efficiency and customer satisfaction. Programmable Logic Controllers (PLC) are at the heart of automated material handling systems in distribution centers, controlling the intricate movements and processes that ensure orders are fulfilled accurately and swiftly. As e-commerce continues to grow, the complexity of order fulfillment processes increases, making the need for updated controls more critical than ever.
For proactive managers this isn’t just a routine check; it’s a strategic move that can make or break the success of their operations. Updating system controls isn’t just about keeping up; it’s about staying ahead. Let’s break down the top five reasons why upgrading control technologies is so crucial.
1. Extend the life of your current automation investment. Substantial resources have gone into selecting, planning, installing, and maintaining your automation infrastructure. Extending the overall service life of your equipment with new controls protects these investments and increases lifetime ROI. The stability of this approach also provides a better vantage point for future changes in your automation strategy.
2. Optimize the efficiency and productivity of your automation. Failures and faults in unreliable material handling equipment (MHE) can lead to painful system downtime and even missed order cycle times. Simply updating the controls in your existing equipment can boost efficiency and productivity. Updating your automation controls lets you rely on your automation day-to-day, ensuring performance in high-volume facilities during extra busy times like peak season.
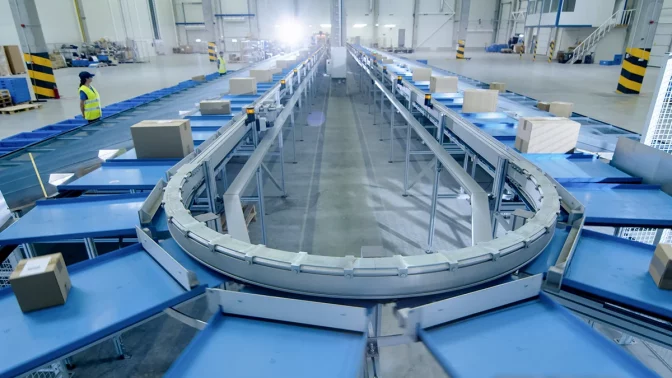
3. Adjust MHE to meet changing business needs. A common misconception is that purchasing all-new MHE is the only way to achieve the functionality needed for changing fulfillment trends. This is not true; upgrading the machine controls of your existing automation can offer extensive enhancements and create opportunities to integrate other automated applications for your business needs. For example, hiring labor is a common challenge for all distribution centers. You may want to integrate a new ASRS with your existing automated conveyor to launch an efficient new goods-to-person methodology. The right controls solution supports these shifts to meet current and future business needs.
4. Move to a more reliable, industry-standard controls platform. Rockwell Automation, formerly Allen Bradley, is a reliable and industry-standard controls platform. Rockwell Automation has an extensive history that has proven stability for being a long-lasting product. Updating your controls to Rockwell’s Studio 500 and current PLC platforms extends the life of your MHE. The Studio 500 platform is extremely versatile, making it easy for updates and migrations. Rockwell Automation’s high-performance PLC hardware, combined with flexible software, delivers solutions suitable for an enormous variety of distribution and fulfillment industries. Older control system components grow obsolete and getting parts can be a challenge, but updating to a more reliable, industry standard controls platform increases lifetime ROI and provides a stable, long-lasting product.
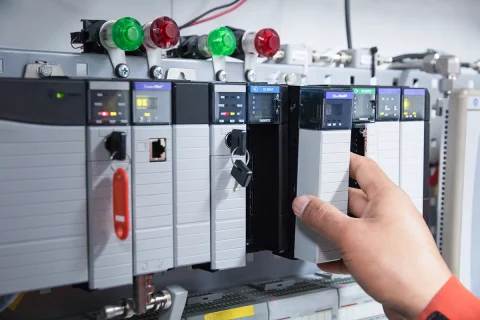
5. More cost effective than full replacement. Retrofitting controls for mechanically sound material handling systems costs less than purchasing all-new equipment. A full replacement might be 30-40% more than updating controls. After installation, you can expect increased productivity and efficiency. When deciding whether to do a full replacement or an update consider the following: ROI projections based on unplanned downtime, as well as the cost of repairs, increased cost of machine parts, and travel fees from support teams, etc. Then compare that projection to the cost of an update.
Increased productivity and efficiency resulting from updating controls can have a significant impact on the overall operations of a distribution or fulfillment center. By integrating a more reliable and industry standard controls platform like Rockwell Automation’s Studio 500, businesses can streamline their material handling systems and minimize downtime. This not only leads to cost savings but also allows for smoother operations, faster order fulfillment, and improved customer satisfaction.
Matthews Automation is a Rockwell Automation Gold system integrator partner with an extensive suite of pre-engineered PLC-based applications. With over 30 years of full-service expertise designing, implementing, and commissioning controls deployments, Matthews Automation can rejuvenate a variety of both new and retired OEM material handling equipment brands.
Let’s talk about revitalizing your material handling automation and fulfillment processes with new controls.