In our recent Rockwell Automation webinar — Transforming Material Handling Operations — Dann Woellert, Software Product Manager, discussed a case study of state-of-the-art automation for a large meal kit delivery service. Below is an overview of Dann’s presentation, which you can watch in the video below this article.
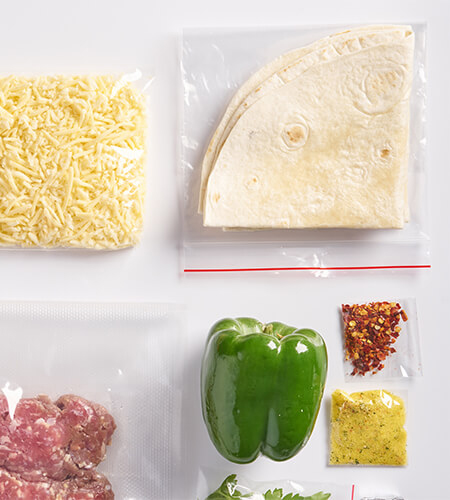
Meal Kit Delivery Services Market
There are many benefits to meal kit delivery services – and the popularity of these services is ever increasing. Ideal for consumers who don’t have time to shop for groceries or plan out their meals, meal delivery services deliver perfectly proportioned ingredients and instructions directly to their doorstep. Customers don’t have to create their own recipes, and the cooking is simple and well explained.
With such a huge and growing market (up to $5 billion market space), the industry continues to gain momentum and become more specialized. Matthews Automation Solutions has helped implement automation in several meal delivery services.
Best Practices for Companies in this Space
- Large variety of meal selections
- Fast delivery due to shipping fresh food items
- Have the least amount of missing items possible
- Minimize substitutions through the use of automated sortation
Warehouse Operations – Software Systems
First, let’s talk about the systems that are in a warehouse operation. On the top of the entire operation is a WMS (warehouse management system) or ERP (enterprise resource planning) system. This is the system that takes orders in from the outside, whether it’s a retail store order or a DTC online order. It sends those orders out in planned waves or batches to Operations to fulfill and is also the system on record that calculates and puts inventory to the accounting system.
How a Warehouse Execution System (WES) Fits In
The warehouse execution system (WES) is integrated software that takes the orders that the WMS puts out into the factory and then manages the flow of the physical items that create the order, such as pick totes, order cartons and pallets. In managing the flow of these physical items, the WES logs every transaction in its flow through the system. In some cases, the WES also creates waves based on client-designated rules and algorithms.
Items include: Bar code reads, divert directions provided, actual diverts, picks, puts, retrievals, labels applied, inductions, etc.
To be most effective in managing flow, the WES controls ALL product moves in a building – not just controlling “islands” of automation, but rather holistic management of the system and a hub of information, creating “Information Anywhere”.
Information Anywhere
In general, information is only useful if presented where it’s needed and when it’s needed, i.e. it’s timely.
Therefore, “Information anywhere” is achievable through the WES because it connects, synchronizes and optimizes warehouse automation, balances workflows, increases systems visibility and creates higher throughput.
Some Functions of a Warehouse Execution System
- Information on available capacity, all stations getting the right amount of work
- Selection of order/batch/wave to release that fits the capacity at that time
- Statistics on performance/rate by area for managers
- Diagnostics in real time
- If provided with business ‘rules’, it can make smart decisions without operator or manager interaction, creating more efficient operations
Meal Delivery Customer System Example – The WES Managed
- Sortation management
- Zone balancing
- Automated order finishing with QC & automated print and apply (PANDA)
- Pallet building, put-to-light
- Item replenishment confirmation with RF scanners
For detailed examples of the processes managed by the WES for a leading meal kit delivery company, watch the video below, and learn about the many functions and types of technologies integrated seamlessly into the WES for intelligent automation, with scalability to meet increases in consumer meal kit demand. Please click on the video player below.
About the Author
Erica Wine, Matthews Product Marketing Specialist, has experience in a variety of roles from education to systems analysis. Automation, design, supply chain, and manufacturing processes have played a central role throughout her career. She is enthusiastic about gardening, the outdoors, art, and technology.